近日,ITvalue发起理事、钛媒体联合创始人刘湘明发表文章讨论“数字化转型成功的标准是什么”,文章提及“数字化转型在过去几年风行一时,以至于很多企业就直接把数字化转型当作了目标,而忘记了它其实只是一个过程而已。这种以过程为结果的打法,注定不会有结果”。作者认为成功的标准依然没有统一答案,但一些观点可拼接出接近答案的轮廓和框架来。
这些观点就包括了:
- “数字化才是真正的一把手工程,因为它的难点在于业务而不是技术”
- “数字化大潮中,技术的后台化趋势越来越明显,能够拉动先进技术向企业渗透的最重要动力变成了深度业务创新”
- “企业的数字化能否成功,其实很大程度上取决于企业家的想象力和愿景”
- “真正的数字化是一个持续运营的过程,是“业务-数据-技术”相互作用、相互迭代的过程。对此,企业的组织和文化都要做出相应的改变。是数字化最难的一个环节”
- “信息化赋能老板,而对终端赋能越彻底,越有效,企业的数字化就越成功”
- “数字化的一个标志是,对外以客户为中心,对内以数据为中心”
通过学习近期媒体宣传的数字化转型案例,小编整理了3家佛山代表企业的历程,来验证数字化转型成功的观点。
制造型企业:
日丰企业集团有限公司
日丰企业集团有限公司创立于1996年,为解决新旧设备产能标准不一、订单交付周期长、人力成本高、信息流转不及时等问题,2014年起将数字化转型提上日程,自上而下推行改革。
转型第一步将集团IT中心转变为数字化转型“大本营”,梳理研发、采购、生产、营销等流程,重构企业基础信息架构,积极与华为、IBM等专业的第三方服务公司合作,陆续引入ERP、MES、CRM等数字化系统。
2017-2020年,IT中心优化改造了企业引进的数字化系统,实现研发、采购、生产制造、销售等全价值链打通。软件优化之余,实现设备自动化。日丰陆续投入10亿元,大量引进、改造生产设备,并大量培训人才适应生产新模式。到2021年,经过8年改造,日丰数字化覆盖到全国5个生产基地,在集团人员总体不变的前提下,整体产出较2017年增加一倍。
在数字化转型期间,日丰一直秉持“一把手”工程推进工作。原本十余人的集团IT中心如今拥有专业IT人才50人,一半人员都考取了PMP项目管理师证书。随着数字化转型日渐成熟,IT中心转变成为创造新业务的部门。6周时间内,利用IBM Garage(车库创新)方法论落地了首个“5G+边缘计算+智慧管网”平台,可对城市管网(含入户管网)进行智能化运营管理。该平台为日丰添加边缘计算能力及增强差异化竞争优势。
转型心得,日丰企业集团有限公司IT中心总监尹浪:
唯有数字化转型得越早、越快,才能给企业带来更好、更直接的效果。企业要将数字化转型视为“一把手”工程,围绕“以客户为中心”的初衷,自上而下推行改革。数字化转型涉及到公司体系变革,需要多个部门乃至上下游产业链等多环节的配合。因此,企业不仅要梳理好组织内部关系和流程,还要在组织机制和平台赋能上积极发力,协同带动企业和上下游企业实现价值重塑。此外,数字化转型是个漫长的过程,企业要有足够的耐心,积极运用外部力量,寻找到适合自身的解决方案,同时,要做好长期且充分的计划,在转型过程中不断发现问题,解决问题。
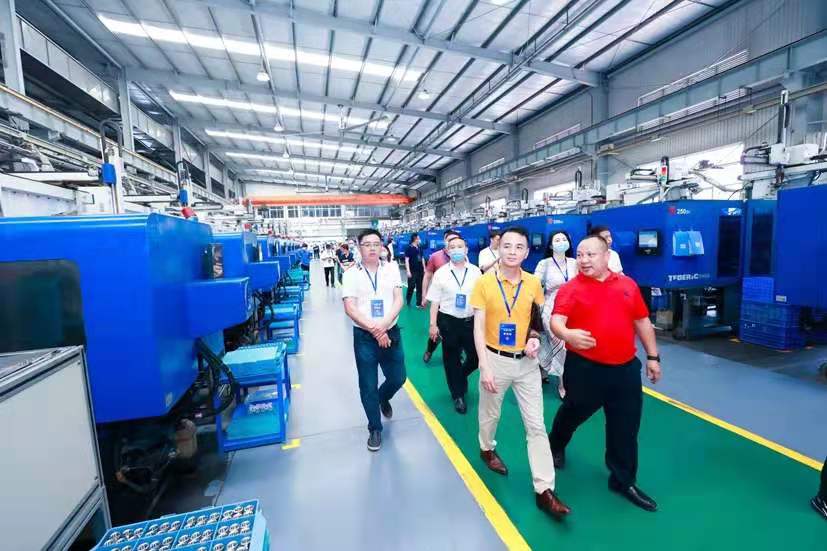
佛山海尔滚筒洗衣机有限公司
佛山海尔滚筒洗衣机工厂利用全流程互联,实现人力投入减少30%、不入库率超70%、订单交付周期缩短超50%等管理效率提升。
2015年,海尔集团建成第一家互联工厂。当年4月16日,海尔全球定制洗衣机暨可视互联工厂发布会在佛山三水举行,从2012年开始筹建的“黑灯工厂”首次正式向外界亮相。该生产线上安装了数千个微小的射频识别传感器,直联MES制造执行管理系统,架构起整个互联工厂的信息脉络。生产环节与生产环节之间,原材料、产品与生产设备之间,都通过传感器、可视摄像头进行数据收集与信息互联,系统对每个生产环节都设定稳定的生产节拍区间,确保各个工位无缝衔接进行作业。
互联工厂不仅做到生产车间内部的人、机、料之间的互联,更强调管理的全流程互联,实现研发设计、原料采购、生产制造、物流配送等所有环节的信息互联。投产后,佛山滚筒不仅实现了产品大规模个性化定制,还实现了交付周期从20多天缩短至7~15天。如今,产品不入库率达到70%以上,大大节约了企业的仓储成本。
自2015年投产以来,佛山滚筒每年都投入大量资金对互联工厂进行升级,包括流程优化、技术升级、效率提升等。如今已建成3条数字化智能化生产线,年产量达300万台洗衣机,整个车间安装的传感器超过10万个。依托海尔卡奥斯工业互联网平台,已搭建起五大信息化系统,实现生产数据、质量数据、设备数据等全采集。当下的佛山滚筒正在谋划建设5G智慧园区,进一步提升整厂管理效率。
转型心得,佛山滚筒工程技术总监包忠伟:
“制造业的核心环节是生产过程,依靠信息技术、智能技术赋能,是制造业企业的重要转型方向。对于中小企业而言,要善于从工业互联网平台借智借力,因应行业特性、工厂特点找到合适的智能化、数字化方案,在转型升级中少走弯路。”
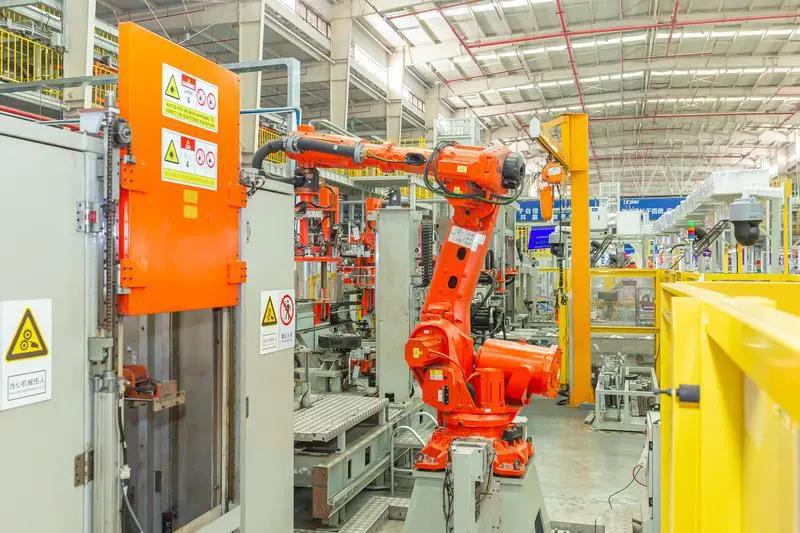
广东顺威精密塑料股份有限公司
顺威精密塑料开发5G+的检测系统减少人力需求同时,解决现有检测效率低下且合格率不稳定的问题。运用先进技术推动车间信息透明及时,打造工业互联网应用标杆示范项目。
在2016年,顺威大规模进行信息化建设工作,实现了从产品研发,到采购、计划、库存、生产、销售、财务、运输等多方面的系统管理。在数字化及智能化工厂建设二期项目中,顺威建立顺威股份注塑环节制造执行系统,使生产过程管理与控制形成一体化,实现了智能自动排产、生产过程管理、工艺管理、品质管理、设备管理、预警管理等。
为解决产品全部依赖人工抽检,每两小时检测一次的模式,发现不合格项则之前两小时的产品可能都需要报废等问题,从2019年,顺威便已开始筹备探索解决方案,携手国内多个研究院历时两年研发,在今年6月底正式开始部署建设5G+贯流AI视觉检测系统,通过使用高清晰度的工业相机在产品线上对产品进行拍摄,采集到的高清图像通过5G网络实时回传至图像AI进行分析处理,判断产品质量是否合格并将结果下发至产线对产品进行标注。通过开发5G+的检测系统,减少人力需求,提高质检的效率、产品的合格率,同时通过及时反馈、及时响应,减少产品报废。
从去年9月开始,顺威开始实施5G+工业互联网+AI智能化工厂示范项目,完成了顺威车间5G专网建设,满足智能制造执行系统(MES)、贯流AI视觉检测系统、具有深度学习能力的自动动平衡检测系统的网络应用需求。9月3日,顺威精密的“顺威股份5G+工业互联网+AI智能化工厂示范项目”进入《2021年佛山市工业互联网标杆示范项目评审结果》的“5G+工业互联网应用标杆”公示名单。
转型心得,顺威集团战略及商务中心总监罗华:
顺威通过数字化转型升级,使车间信息透明、及时,大幅提高了设备利用率,降低了生产成本。未来,顺威将继续以市场变化、客户需求为指引,推动制造与数字技术深度融合,增强市场竞争力。
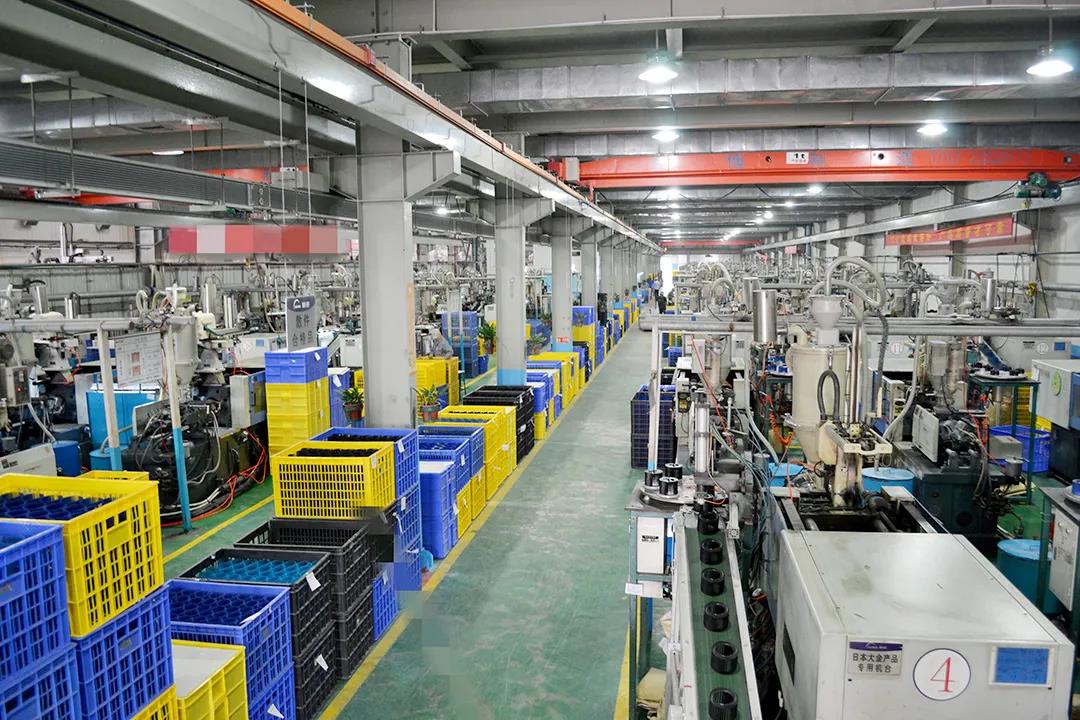
来源:佛山日报、日丰企业集团有限公司、南方日报、广东顺威精密塑料股份有限公司、佛山科技、佛山高新区、佛山滚筒创客之家
智汇+工业创新成果推广平台整理发送